
Here's a trick I learned: Cut off the loop end of the brush and put it in a cordless drill chuck. You do not want to put epoxy into a dusty hole because you run the risk of not getting a good bond. I blow it out with the air, put in the brush and twist it to remove any loose material on the sides and then blow it out again. Using compressed air (or if unavailable, a heavy-duty plunger device), along with wire brushes made for cleaning out drilled holes, you need to properly clean and blow out the holes prior to putting the new steel in place.

In that event, I choose a new location for the hole, typically diagonal down and over, approximately 1 inch. On occasion you'll find yourself encountering existing steel. To properly accommodate the steel size, the holes I drill will be 5/8-inch in diameter, drilled at a 45-degree downward angle with my roto-hammer. It's much easier to bend than grade 60, which is very rigid and commonly used in foundations. I always use #4 steel, preferably grade 40.
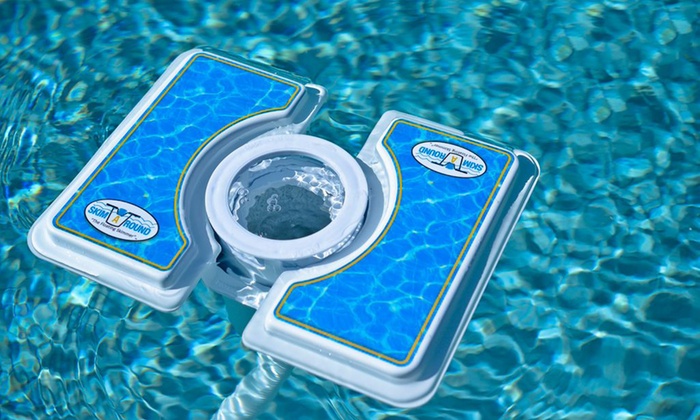
On this project, we retained the old steel in conjunction with the new rebar for added strength.

Following the skimmer's plumbing installation, you will need to re-pressurize the line in order to ensure the integrity of your work. Sometimes it's obvious where the fracture is located, other times it will require a pressure test to cause the leak to present itself. NOTE: If a skimmer is being replaced because of a pre-detected plumbing leak, it's important to conduct a follow-up pressure test after all of the skimmer's plumbing have been exposed.
